Steam Traps Case Study – Water Treatment
Manufacturing company gains cost savings on steam loss and reduced carbon emissions immediately after installing DCO Steam Trap Monitors.
SUMMARY
Steam specialists overseeing a suspension component manufacturing plant outside of Birmingham contacted DCO Systems for steam trap monitoring solutions.
Their client moved to a new facility and invested in new equipment, which was being combined with the existing steam system. This led to some faults appearing in steam components, and identifying where these faults was problematic. A monitoring solution was required to find the source of steam leaks, while eliminating manual testing and providing real-time insight into steam trap performance and operation.
Steam trap monitoring devices were installed and several failed traps were identified. This in turn created an alert for the engineering team and they were able to fix the issues immediately.
As DCO’s products are scalable, the existing infrastructure allowed over 100 monitors to be installed. As a result of identifying failed traps immediately, this customer gained automatic cost savings on steam loss and reduced carbon emissions.
WHERE
Manufacturing facility in Birmingham, UK
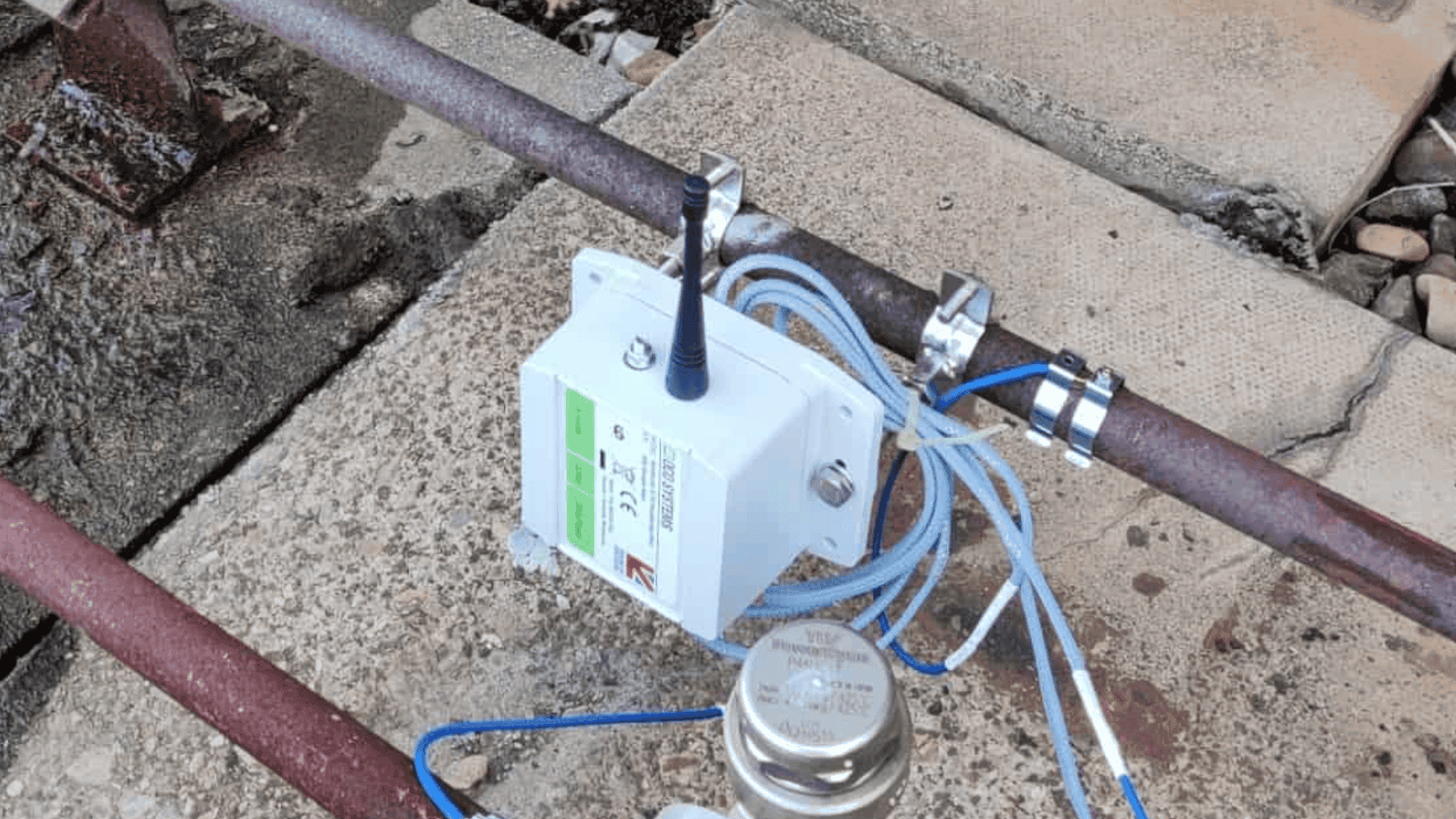
OVERVIEW
After moving facility, the steam system in this facility comprised of old and new components which was causing come failures within the system and due to the size of the system the occupiers were finding it hard to locate the faults.
Steam specialists were called in to help identify the problems as the faults in steam components could impact both the site’s emissions and product quality. A monitoring solution was needed to eliminate manual testing and provide real-time insight into steam trap performance and operation.
In addition, the plant manager required real-time integration of the steam trap monitoring solution with existing onsite monitoring systems.
CHALLENGES
- The steam system within the manufacturing plant was unique, the layout consists of a set of press units, housing several traps each, steam boilers and steam distribution lines.
- Furthermore, the difficulty of accessing each installed unit meant that the monitoring solutions should avoid fixed-wiring and a battery-free solution was preferable
SOLUTION
DCO Systems offered a simple monitoring solution specifically targeting steam traps.
The monitoring units are powered using energy harvesting technology which generates power from the heat produced from the steam system.
Because the system had a unique set-up, DCO’s team was able to identify that most of the monitoring could be achieved using the BASE model. This meant that 80% of the traps could be retrofitted with DCO’s out-of-the-box solution. For the other 20% of traps, using DCO’s modular technology, monitors could be adapted to the specific site requirements.
Furthermore, DCO also installed a gateway system to collect, record and analyse the data collected. Upon first start, detailed temperature profiles were recorded to establish normal and baseline operational conditions.
CONCLUSION
Within a few days of using the steam trap monitors, several failed traps were identified. This in turn created an alert for the engineering team and they were able to fix the issues immediately.
Furthermore, the manufacturer is currently installing several new press units, all of which will be equipped with DCO’s steam trap monitoring solutions for their new traps.
As DCO’s products are scalable, the existing infrastructure will allow more monitors to be installed. As a result, identifying failed traps immediately will translate into automatic cost savings on steam loss and reduce carbon emissions.