Energy Savings in Water Treatment Part 2 – Steam Boiler
Continuing with our series where we look at ways which can help save energy in your water treatment, this month we look at Steam Boilers.
Facilities with large steam boilers can save thousands in energy and maintenance costs each year by improving the energy efficiency of their steam or process heating systems. Boilers get plenty of use, especially during the cold months, and efficiency is a necessity for the environment and your budget.
When your boiler, steam and process heating isn’t working together efficiently, they can add up to 60% to your energy bill.
But there are ways you can reduce the amount of energy you use in the process, which can:
- lower your gas bill
- cut your maintenance costs
- decrease your greenhouse gas emissions
- improve safety and work conditions for your employees.
A great place to start lowering your bills is to look at how recently you performed boiler maintenance and how efficient your boiler is.
The majority of heat lost in your boiler is in the stack or boiler water. The goal is to create conditions that generate the smallest possible amount of flue gas at the lowest possible temperature. This results in increased boiler efficiency.
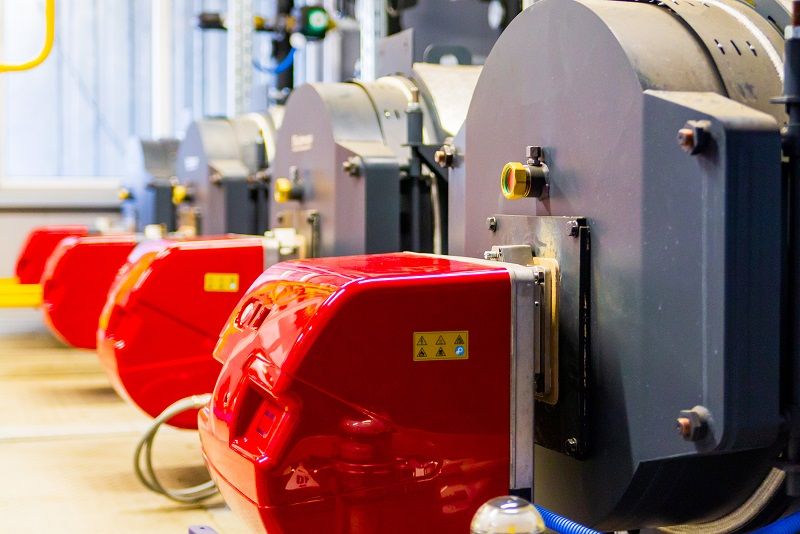
Lower the Stack Temperature
Lowering stack temperatures could be as simple as a day/night set back. This lowers the operating pressure for steam boilers and the operating temperature for hydronic boilers when idling at night or mild days
Tune the Burner Regularly
Another common issue is not getting the right amount of air. For proper combustion of fuel inside the boiler, a certain amount of oxygen is required.
If too little air is present, the carbon in the fuel will be oxidized, making carbon monoxide. This causes less heat to release because the fuel isn’t completely burned, which lowers fuel use efficiency. Low air generates soot, smoke and carbon monoxide, all of which are dangerous.
Too much air also reduces efficiency. The extra air comes in cold and sent out the stack hot, wasting heat.
An optimal process provides just enough air for the fuel to burn safely.
To achieve this, we measure the amount of air needed with an O2 probe. We insert the probe into the stack while we tune the burner for optimum efficiency.
Change the Burners
Weak burners put stress on your boiler and cause it to run inefficiently, so replacing them soon after they begin to deteriorate will reduce your business’s heating costs and energy consumption.
Ask your technician to check for wear and tear on linkage components, misaligned burner heads and adequate combustion air at every maintenance appointment. They may also recommend energy-efficient parts to replace the problematic components.
A linkageless burner upgrade can normally be performed without replacing the entire burner. This can improve fuel-to-steam efficiency and combustion performance as much as 5% and can usually pay for itself in a short period of time.
Insulate Your Valves
Many plants remove the insulation on valves in the boiler room for maintenance and never put it back – however, exposing these large valves to the air causes a lot of heat loss and can make the boiler room unbearably HOT.
Insulating these valves can save significantly, improve boiler room comfort. The blankets also reduce the risk of burns while still allowing easy access for maintenance.
Return Condensate to the Boiler
Condensate forms as the steam transfers its heat and condenses, it is irresponsible to waste this by product.
The clean water is without dissolved solids or gasses that are ready for use again in your boiler. The water is already hot and therefore requires significantly less fuel to make it into steam again.
Reusing the condensate also reduces how much cold makeup water, chemicals, and treatment is required for your boiler. Lastly rerouting condensate back into the feed water system can reduce wastewater treatment and sewer costs.
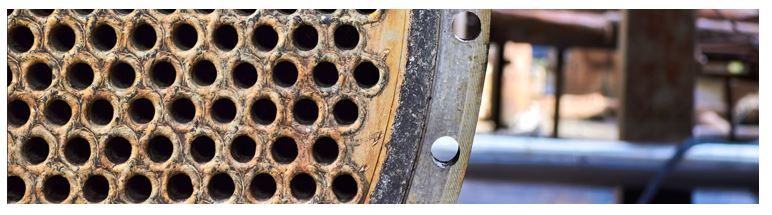
Recover Heat from Boiler Blowdown
Much like the return of condensate to the boiler, recovering the heat from the boiler blowdown can increase boiler efficiency.
The blowdown valve is used to remove boiler water which contains soluble and insoluble solids. It helps reduce the level of dissolved solids in the boiler water to prevent the boiler scale.
Unfortunately, when it removes hot water, it also wastes energy. Installing a blowdown heat exchanger, flash tank or combination of the two can help recover some of this energy for your boiler system. Using heat recovery to cool down the blowdown and heat up your make-up water will improve energy efficiency.
Control Blowdown Rate
Blowdown removes impurities, like water hardness, from the boiler and is required to keep the boiler surfaces clean. However, blowdown also removes heat from the system.
Water enters the system cold, is heated up to the boiler temperature, and leaves through the blowdown. Some boiler systems have continuous blowdown that does not change with boiler load. To control the heat sent down the drain, blowdown should be limited only to the amount necessary to control the dissolved solids. For serious savings, control dissolved solids with an automatic blowdown valve. If you blow down the boiler when it regularly, you can save a lot of energy. This also reduces risking damage to your boiler from the scale.
Reduce Steam Usage
The best way to save on fuel and electricity to your boiler is to reduce steam usage in your processes. Insulating piping and tanks heated by steam, for example, can significantly reduce steam usage, and therefore, fuel usage. High-pressure condensate systems can reduce steam usage at your deaerator AND fuel usage in the boiler.
Schedule Professional Maintenance
And ofcourse, the best way to ensure continued boiler efficiency is by setting up a professional maintenance schedule.
Your contractor will inspect it for signs of damage and perform repairs to boost its functionality and will let you know when it’s time for a replacement. It is best to have regular maintenance performed at least quarterly in addition to the required annual inspection. Deficiencies can be discovered during the quarterly inspections and remedied prior to the annual inspection so the boiler is not red-tagged by the state and your boilers can be put back on-line without delay.
Ensuring your boiler efficiency is key to controlling your monthly bills. Having a knowledgeable company service your burner, boiler, and steam system regularly will help you ensure that your boiler is as efficient as possible.
Let Aquachem help you prolong the life of your equipment and work toward preventing repair costs down the road. If you need help, check out the contact us page and send us a message!