Energy Savings in Water Treatment Part 1 – Cooling Towers
Issues around energy consumption are of growing importance in the current climate with higher energy and production costs.
Companies today are keeping a close eye on their costs so they can identify areas where energy is wasted and introduce cost saving measures if possible.
When it comes to managing a building or facility, water management is often not seen as a high priority and so don’t realise the importance of sustainability management and how it can have a massive impact on energy savings within your building.
In this series we will take a look at some of your water treatment equipment and how they can help your business produce energy savings for your business.
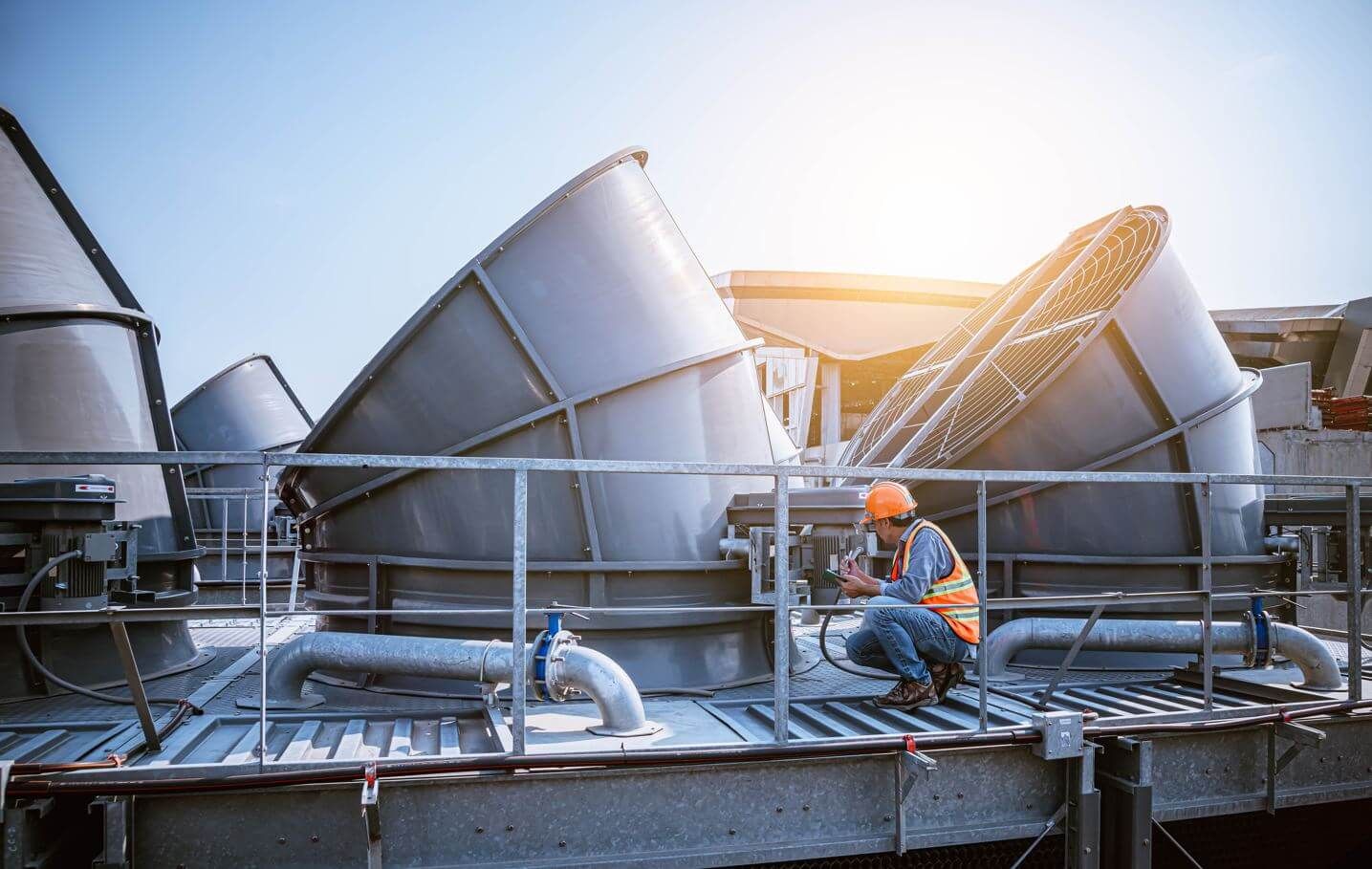
Today we take a look at Cooling Towers.
Over time a neglected cooling tower’s leaving water temperature will increase, raising energy costs by up to 6% for every 2°F increase. However, a well maintained cooling tower will continue to function at the original optimum efficiency, keeping energy costs low.
Cooling towers are an important part of many systems and there are many ways in which to make a cooling tower more energy efficient including making sure the tower is sized correctly to start with, incorporating better fans, including variable-frequency drives (vfd’s), adding new or more efficient fill, or using a new set of nozzles to give better distribution over the fill.
Let’s take a closer look;
Tower Size
Ensuring you have the correct size tower to begin with is invaluable. Calculating the best size of tower for your system is crucial for ensuring the tower performs as expected and maintains the system efficiency and function. Because HVAC systems rely on towers to keep their temperature at a safe level, an undersized one that isn’t able to adequately cool the temperature can easily cause system failure.
Fan Control for Energy Efficiency – Fans, Fill, and Nozzles
If the incorrect size has been selected then it makes sense to bring the existing tower to its fullest potential, which may involve extensive renovation.
Fans
The fans are the number-one user of power in a cooling tower, and that’s the first place to look for energy savings. Engineers may want to consider two-speed motors, as they use about 1/6 of the power at low speed.
It’s also possible to use vfd controllers for the fans and pumps in order to reduce the parasitic power at low heat loads. There is an advantage because fan power varies as the cube of the air rate (cfm), and thermal performance varies directly as the air rate.
Fill
The fill is another component that can help save some energy, many old towers have splash-type fill, which is not as energy efficient. If the system is not normally subject to water scaling, algae, or other contamination, some towers may benefit from a change to film-type fill. (In some cases the more modern film-type fills can plug due to water contamination from algae, dirt, minerals, etc.) If this is done, it is necessary to consider all of the parts of the tower – especially the fan and nozzle systems.
Nozzles
As for the nozzles, in a crossflow tower, it is important that the nozzles properly distribute the water over the fill. Better distribution can usually only be obtained by adding distribution decks directly below the nozzles; however, in a counterflow tower the nozzles can contribute as much as 25% of the cooling, and changes to the nozzles can either help or hurt.
There are also some general maintenance checks you can do to ensure your cooling tower is operating correctly and efficiently. Save on electricity costs with these simple preventive maintenance tips for cooling towers. Routine maintenance also helps to conserve water and extend the operating life of cooling equipment.
- Check overall cooling and listen for any uncommon noises in the system to establish a baseline of possible issues.
- Before beginning any hands-on work, be sure to follow proper lock-out/tag-out procedures and disconnect motor switches to protect your safety and that of other personnel.
- To keep the system free of potentially problematic materials, inspect and clean debris from strainers.
- To avoid a build up of scale and increase capacity, inspect the water-distribution system and check for dry areas over the fill-coil section. If the surface isn’t fully wetted, check the nozzles for cracks and clogs.
- To conserve water and reduce air entrainment, be sure the make-up water supply is at the appropriate, pre-determined level.
- To prevent accumulation of solids in recirculating water, adjust the bleed rate according to your local water-quality and evaporation-rate regulations.
- To assure reliable service in a gear-driven system, routinely check for and maintain, correct oil level, oil quality and shaft alignment, per the manufacturer’s’ recommendations.
- Lubricate fan shaft bearings every three months, at a minimum. Consider installing automatic bearing greasers to eliminate monthly bearing maintenance.
As with other systems in a plant, good maintenance habits will go a long way in preventing failures and extending the life of your cooling equipment.
Looking for other ways which can help save energy in your cooling tower? Talk to us today.