Production process sped up by 7 days using ATP Pens on surfaces
SUMMARY
Our client produces different whiskey & liqueurs where cleanliness is top priority.
They mentioned to one of our engineers they were losing days, sometimes up to 1 week of production when they switched from bottling cream liqueurs to whiskey because in order to avoid contamination of product the cleaning standard required was extremely high.
They were using the “plate culture” method which takes 48 – 72 hours to show results, and when these results came back to show the cleaning was not up to standard, the cleaning had to take place again – meaning the swabbing & waiting had done again also.
Our engineer advised them we have the ATP luminometer which provide you accurate results in 10 seconds.
After purchasing a the meter the very quickly realized how much time, labour and money they were saving.
WHERE
Manufacturing Facility in Co. Tipperary
OVERVIEW
Our clients produce, bottle and pack whiskey & other liquers in the same facility where a high standard of cleanliness is imperative to ensure there is no contamination of the product.
The site were using the “plate culture” method to measure the level of bacteria on surface. This process involved taking a swab of the surface and then placing in an incubator for 48 – 72 hours to obtain results. This method is a common practice in all industries but is time consuming and leads to loss of production.
One day when our engineers were on site, they mentioned that they had lost a week of production due to cleaning. Their first batch of results came back stating that there was still a number of bacteria on the surface. The cleaning process was repeated, swabs taken again with another test taking place. After another 2 ½ days the results showed that the bacteria had been eliminated and set up for production could begin.
This particular site would take over 3,000 sites each month. This results in additional labour in preparing the samples & testing, cleaning processes need to be repeated days later – even on weekends if required.
Our engineer advised site we have ATP luminometer meters which measure the level of bacteria on a surface in 10 seconds.
Site initially purchased one of the meters and on Day 1 noticed how much time they can save by using this product.
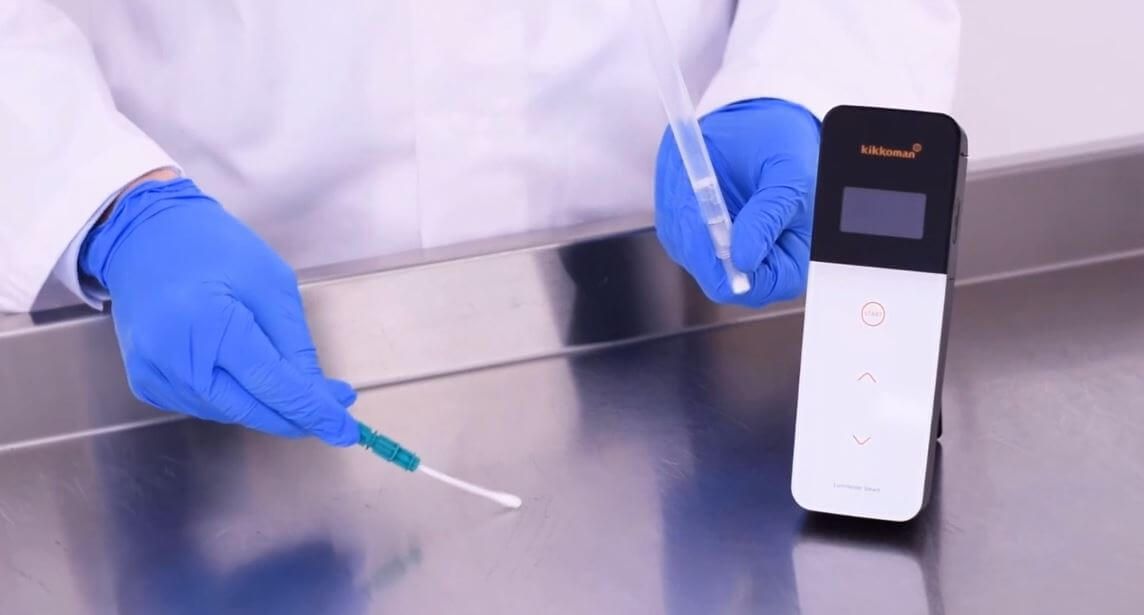
OUTCOME
This site now saves time, money while speeding up production. They can produce accurate bacteria readings in 10 seconds and can rectify any issues immediately instead of in 2 / 3 days time. The STP reader does not only measure ATP but also ADP & AMP – giving better results than the “plate culture”.
TIME SAVED
- Not waiting days for results
- If results show bacteria still present additional cleaning can be carried out immediately
- Labour not required for arranging additional cleaning as they are there
- Personnel not required to label / plate up swabs
- Less administration required
MONEY SAVED
- No loss of production
- Cleaners not required to come days later or weekends
- Less labour required
- Less administration hours required
SPEED UP PRODUCTION
- No waiting days before production can resume
- Cleaning process issues can be identified straight away with new procedures put in place, meaning the next time cleaning results should improve
WHAT WAS DONE?
We gave site a demo of how our ATP meters worked showing them how bacteria readings could be shown after only 10 seconds
Site purchased and ATP meter to speed up cleaning and production processes at their facility
On day one the fist lot of samples were taken showing that bacteria was still present at some locations
Cleaning continued and another swab was taken
Within 1 hour they were able to continue their production line as they know all surfaces were clear
**this would usually have taken days resulting in addition time, money, labour and STRESS!
Site purchased another meter to help quicken the process even more
CONCLUSION
By introducing a small piece of innovative technology, this business saved thousands of euro and could introduce time saving methods to their processes.
These customers continue to be very happy with their meters and are still impressed at how useful they have been. Cross contamination is a big no when working in the food and beverage industry and these ATP meters can give you peace of mind that your surfaces are safe.